A VIP reception desk made of waste wood
On the 6th floor of the Johan Cruyff ArenA, at the entrance of the VIP area, there is a brand new, luxuriously executed hospitality desk. You wouldn't say at first glance that it's made of waste wood. The desk is designed and built, with the help of industrial robots, by researchers and students of the Amsterdam University of Applied Sciences.
ROBOT STUDIO
The desk was made at the Robot Studio of the Faculty of Technology, guided by the Digital Production Research Group. It is the end result of 2 research projects funded by the KIEM-ce funding of the Taskforce for Applied Research SIA. It is a first step towards designing and producing new furniture and objects from waste wood on a larger scale.
Saved from the incinerator
"From wood trader Fijnhout we got a lot of 300 pieces of residual hardwood. Great quality wood, but in all kinds of different shapes, sizes and colors. Normally this wood is chipped and burned, because you can't make anything with all these loose pieces," says Marta Malé-Alemany, senior lecturer and researcher at the AUAS Digital Production Research Group.
"In our previous KIEM Circl-Wood project, we developed a method in which the computer can make a 3d model based on the pieces of wood available, previously scanned by a robot. With this method we could make the design for the desk based on the pieces of wood from Fijnhout."
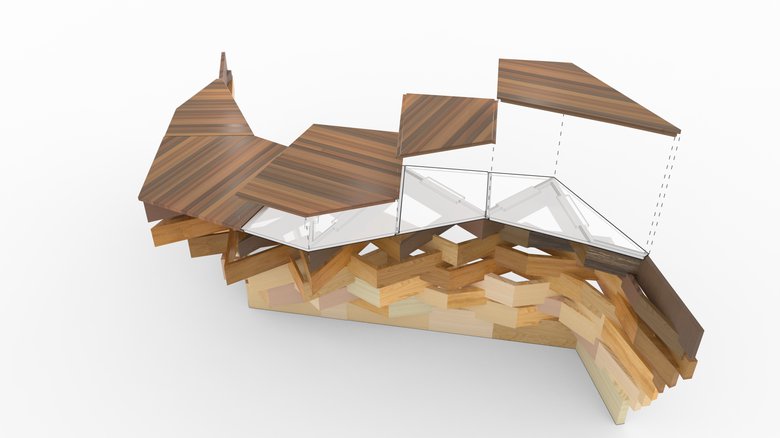
The design for the reception desk by AUAS Robot Studio
Every piece in its right position
Project leader and lecturer-researcher Marco Galli adds: "Our algorithm arranges the pieces, as it were. We can adjust the parameters of the overall design. These are the dimensions, for example, but you can also prioritize that you want to place light pieces at the bottom and darker ones at the top of the design. The algorithm ensures that every piece of wood gets the most optimal place in the design. Even the counter tops are made of residual wood. If you still want to make the overall desk design a few centimeters higher or wider, the program will recalculate the arrangement of the pieces in a few seconds."
Unique connection structures
"The computer also generates the joints by which the blocks are connected together, like a lego block. Each of these connections is unique for each wood piece. In this way, no screws or glue need to be used, which is a more durable solution. The robot from the Robot Studio then cuts the pieces to size based on the computational design. Our Robot Studio interns made the construction together with the robot.
KIEM-ce
The KIEM-ce subsidy of Regieorgaan SIA is intended for 1-year research into circular economy. It also aims at making new connections between universities of applied sciences and companies and other partners in the area of circular economy.
Robo Wood
In addition to Circl Wood, the other project with which the counter was created was Robo Wood. This project was intended to investigate the custom tools needed together with project partners for handling and custom sawing all the wood the pieces, using the robots.
Before that, it was done by hand. That was so labour-intensive that scaling up would never be possible. The research has shown that this is possible to use robotic technologies for upcycling wood.
The results of these 2 projects came together in the reception desk. In fact, on the basis of the KIEM grant, it would only remain with a design, after all, that money was earmarked for research. But our partners of the Johan Cruyff ArenA were so enthusiastic that they actually extended our involvement with a direct commission, to put the counter into production.
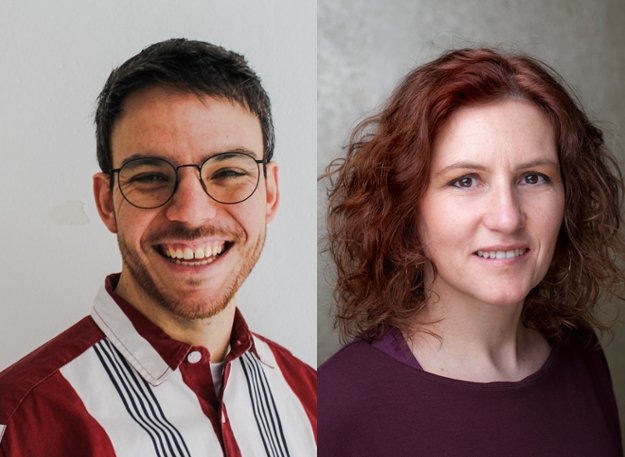
Marco Galli Caro and Marta Malé Alemany
Beyond a hobby
The next step is to be able to do this on a larger scale, so not with 1 object and 1 residual wood lot, but with larger quantities. The methodology should make this possible, but further research is still needed to optimize it. To start, we want to investigate the design opportunities and business case for making circular wood applications for the horeca sector. This is a sector that understands the value of customization and can help in applying circularity.
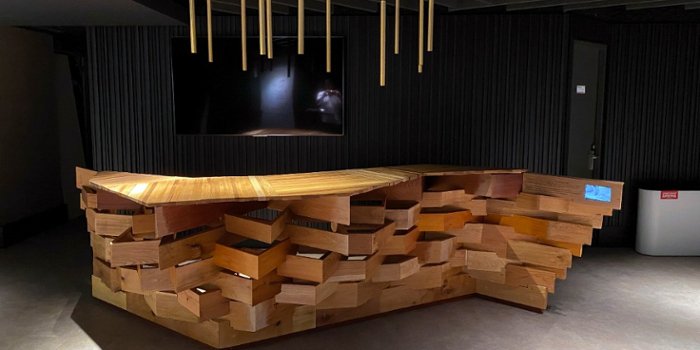
The desk at the Johan Cruyff ArenA
A lot of KIEM fundings
Malé-Alemany explains: "In the Digital Production Research Group of AUAS, we make a lot of use of the KIEM fundings of Regieorgaan SIA. Above all, we appreciate the flexibility of these type of grants."
"Our type of research is often a bit pioneering and trying out. Because the duration is short, it makes it easier. The arrangement also makes it possible to work together with a lot of different partners, like, in this case, the Johan Cruyff ArenA and the wood processing companies."
KIEM-projects as a main ingredient
Also, writing an application takes a relatively short time. "By pioneering and combining the results of various KIEM studies, we have not only been able to create the desk, but also to meet good partners for future projects. With them and other parties, we now want to scale up in a larger RAAK-mkb project. For us it works like this: the results of the KIEMs are our ingredients, RAAK projects are our recipes."
Partners and collaborators
Partners in the projects: JC ArenA , Heineken Interior Design , Nijboer Interieur and Amsterdamsche Fijnhout.
Digital Production Researchers: Liselotte Van Dijk, Sebastian Yap, Erno Langenberg
Robot Studio Interns / Design and Production: Lennox Clarke, Fabian Shreurs, Liam Kelly, Stijn Oostra, Nick Stam, Valentijn Bors, Jakob de Koning, Cameron Roeten, Djani Cerneus, Jurriaan Nuijs, Tanie Ali, Finn Buskermolen and David ’t Lam.
Pictures students: Sander Heezen